A guide to food traceability methods
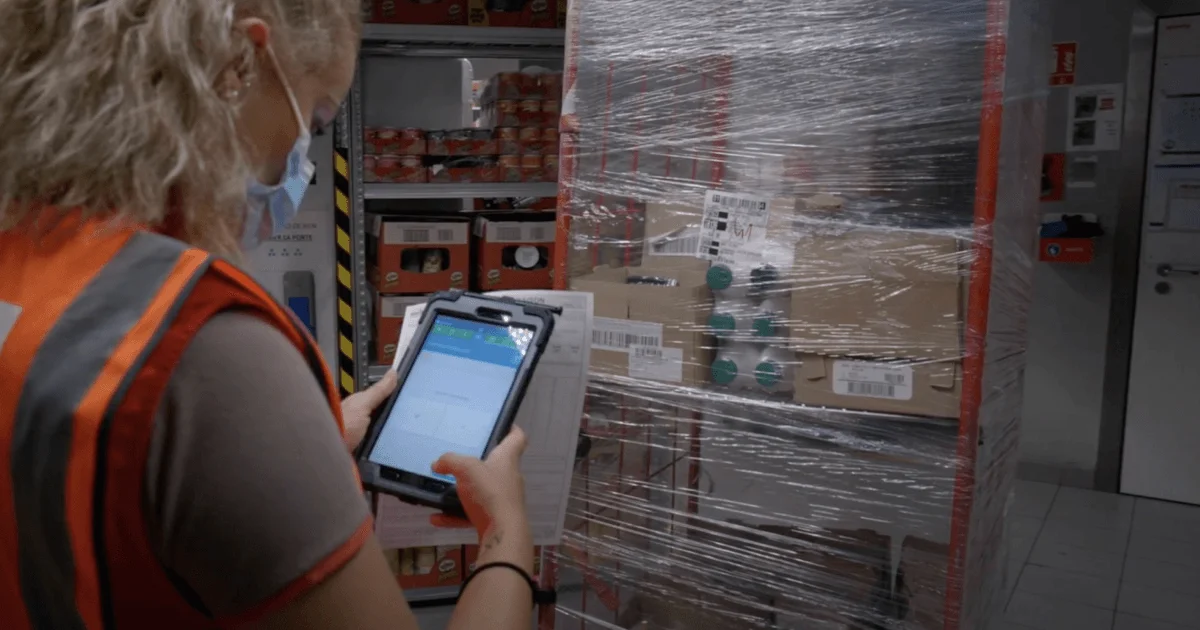
Food traceability is one of the key levers used by foodservice professionals to ensure food safety.
Regulation (EC) no. 178/2002, the key text of food legislation, known as the Hygiene Package: the Food Law, states that :
"Experience has shown that the functioning of the internal market can be compromised when foodstuffs cannot be traced [...]. Consequently, it is necessary to set up, in food businesses [...], a comprehensive food traceability system [...] enabling targeted and precise withdrawals to be carried out or consumers or official inspectors to be informed, and thus avoiding the possibility of unnecessary and greater disruption."
Traceability therefore plays a crucial role in controlling food safety risks, not only throughout the food chain, but at every link in it .
It also represents an operational challenge for catering teams.
In fact, it requires both time and rigor to systematically list the right traceability elements and, in due course, to retrieve this information quickly and efficiently.
Through our experience with major players in the foodservice industry, we have identified several ways of meeting these traceability requirements. In this article, we present them to you, with their advantages and disadvantages.
What are the advantages and disadvantages of each traceability method?
We'd like to take you through some of the most common types of traceability used in the foodservice sector.
Some emphasize the low workload required by field teams to enter this information on a day-to-day basis, while others focus on the speed of traceability searches, as well as the finesse and quantity of the information provided.
As these methods are not based on any technology or digital tool, they do not allow for monitoring other than on site by direct management. They require a great deal of time for archiving and traceability. As a result, they make it difficult to react quickly in the event of a problem, and do little to limit risk.
When this method is used in a complete catering network, the impossibility of ensuring that traceability is carried out on a daily basis at each site poses a definite risk to the brand as a whole.
This method relies on the physical cutting of labels and their physical storage in archive boxes for long periods. It is sometimes combined with manual entry of label information into a dedicated register.
The manual cutting process is relatively straightforward, but although fun, it takes up a lot of the teams' time.
Archiving these non-digitized labels is cumbersome, time-consuming to file properly, and can be a health hazard when the labels have been in direct contact with the product. What's more, in the event of a problem at the archiving location, there's a high risk that this information will be lost over time.
With all the information stored manually, finding a specific label can become a nightmare, especially if the archive is vast and poorly organized. This method requires on-site visits, and takes a fair amount of time to find the information you need at a time when you're already under stress.
This method involves digitizing traceability photos, but without a digital solution. Typically, on-site teams take photos of traceability labels using a digital camera, and manage their archiving using a traceability system with folder trees on a computer.
Photo scanning is the fast part of the process. It saves teams time and eliminates the need to handle labels.
Archiving, on the other hand, is more tedious. You have to connect the camera to a computer, extract the photos and file them "by hand" in the right folders. Even if this phase can be carried out once a week, leaving photos on a camera for long periods of time presents a significant risk of data loss.
The speed with which traceability information can be retrieved with this method will depend on the file organization system in place. In all cases, no information other than the photo itself is available, and the search will take time. Generally, files are sorted by date of preparation (one file per day). When this information is missing or incomplete, the search becomes complex, if not impossible.
Archiving data on a single "local" computer represents a major risk of data loss. Setting up a regular backup on an external disk physically brought to another site reduces this risk, but makes the process more cumbersome and time-consuming.
These digital traceability methods give you greater control over your risk.
These solutions generally equip field teams with a digital tablet containing the entireself-checks HACCP plan.
For traceability, the tablet's built-in camera enables labels to be scanned directly into the application (by taking a photo and/or scanning an EAN128 barcode), along with the necessary contextual information: dates, recipes, raw materials, finished product, etc.
What's more, since the data entry itself is digitalized, reminder systems and tracking systems can be set up. This will help to ensure that traceability is correctly entered on a daily basis, and thus greatly reduce the risk of non-fulfilment.
With automated, synchronized filing and archiving of information on remote servers, data can no longer be lost. Information will always be available, even remotely. So there's no need to worry about day-to-day archiving. This saves a considerable amount of time.
Digital technology offers another interesting opportunity: flexibility in the choice of methodology. In fact, because these solutions can be parameterized, each quality manager can choose what needs to be entered on site to ensure traceability in line with his or her brand's requirements.
Above all, the most advanced digital solutions are agile. It is then possible to adapt a new methodology over time if brand requirements change, or if a methodology does not present a satisfactory level of adoptability with field teams.
This is what happened at one of our customers, who deployed our Eezytrace solution on its network of several hundred sites.
To reinforce traceability, their first method was to ask the field to enter as many elements as possible each day.
But a study of the solution's adoptability on its sites showed that the data entry workload for its teams was insurmountable.
The method was immediately reviewed and updated remotely on the tablets to lighten the load of data entry for traceability. The amount of information required was limited to the essentials. The customer thus maintained a level of risk control in line with its standards, while allowing its teams to devote more time to other aspects of their business: customer reception, cleaning, maintenance, etc.
This method consists of using a digital solution to collect traceability photos by attaching them to the data of the date of capture and another which can be: the date of unpacking of the product or manufacturing or consumption.
Recording traceability information (photos + date) is as quick as using a camera, but it also enables automatic archiving of this information in a database. As the information captured in addition to the photos is limited to the date of unpacking, manufacture or consumption, the entire process requires little effort on a daily basis.
The traceability search will be carried out in the digital solution, and will enable traceability photos to be quickly filtered according to previously entered dates. The search can therefore be effective when this information is known. On the other hand, if you want to search for traceability based on a finished product or a material, for example, this will be more time-consuming and tedious.
This method involves using a digital solution to collect traceability photos by attaching them to the finished product and its associated information: DLC of the finished product and sometimes the date of manufacture or consumption.
The user first selects a finished product, then takes all the label photos of the raw materials used to make the product.
The advantage of this method is that it doesn't overload the data entry process, making traceability searches much more efficient.
Traceability search options are extended to include the finished product and the best-before date of its products, in addition to the dates entered. So it will always be easy to find a traceability.
This method consists of using a digital solution to collect traceability photos by attaching them to the raw material and its associated information: product unpacking, manufacturing or consumption date, supplier best-before date, secondary best-before date.
The user first selects or enters a raw material before attaching traceability elements: dates, supplier and secondary BBDs, and traceability photos. This method is more restrictive than the 2 previous digital methods, as there is more data entry, but the level of detail provided will enable an extremely rapid traceability search.
Traceability searches become very efficient, as users can search for traceability information from several angles: raw materials, date of entry, best-before date.
This method consists of using a digital solution to collect traceability photos by attaching them to the ingredients of a recipe and its associated information: product unpacking, manufacturing or consumption date, supplier best-before date, secondary best-before date or even batch number.
It can be used in conjunction with the Recipe module, which enables all recipes to be pre-configured to facilitate production directly within the application.
For the same effort as the previous method, this method allows you to enter traceability information in fine detail. Automatic re-entry of opened products (optional with QR-Code) can greatly reduce data entry time.
As with method 3, data entry takes longer, but provides a wealth of detail. QR Code management of opened products saves time by avoiding the need to re-enter product details.
The traceability search is highly efficient, with all elements entered being searchable, making it quick and easy to find traceability information, particularly by batch number.
There's no such thing as ideal traceability. Even if the regulations are the same for everyone, the method is the one that best suits your brand requirements, the time your teams can really allocate to it, and the effort you want to put into traceability research.
So there's no one-size-fits-all solution that's right for everyone (and then it wouldn't be right for you), and it's up to you to assess your unique needs and capabilities to select the most appropriate system.
The key is to strike a balance between costs, benefits, compliance and ease of use, while keeping in mind the importance of flexibility and adaptability.
Digital solutions, such as Eezytrace, enable you to adapt to your requirements, even if they change over time and whatever the size of your network. In fact, modifications to settings, such as the type of traceability, can be deployed remotely in just a few clicks on users' tablets, wherever they may be.
Traceability plays an essential role in controlling food quality in your company, and extends far beyond the food chain.
The right choice of traceability system will make the difference between
EFFECTIVE RISK CONTROL
VS
LABORIOUS, INEFFICIENT MANAGEMENT
Digitizing traceability is one of the building blocks for improving food safety. It offers substantial advantages in terms of efficiency, responsiveness and risk control, transforming the way companies in the sector approach these issues.
Other challenges remain in this area, such as the quality of traceability information on photos.
For a traceability photo to be compliant and useful when the time comes, it must contain the necessary information: product name, supplier name, best-before date, batch number, stamp for products of animal origin, etc., and first and foremost be a photo of a label and not of anything else.
To limit the risk of non-compliant photos, some Quality Managers now spend part of their time randomly checking photos taken by field teams at their sites. Without being able to do so exhaustively, this enables them to verify good traceability practices on site.
At Eezytrace, we're tackling this issue from the angle of innovation. We are working on an automatic AI-based label recognition algorithm. This project will lead to functionalities that will enable massive analysis of label photos, or of an aid at the moment of taking a label photo, to ensure that they are systematically compliant, and thus totally limit the risk of unusable photos and therefore of unrealized traceability. This will also mean that Quality Managers will no longer have to look massively at traceability photos to be reassured.
To find out more about our forthcoming innovations and Eezytrace news, subscribe to our newsletter.
To go further in risk management, download our step-by-step guide of 36 pages. (Available in English soon)