Interfacing a HACCP application with company software
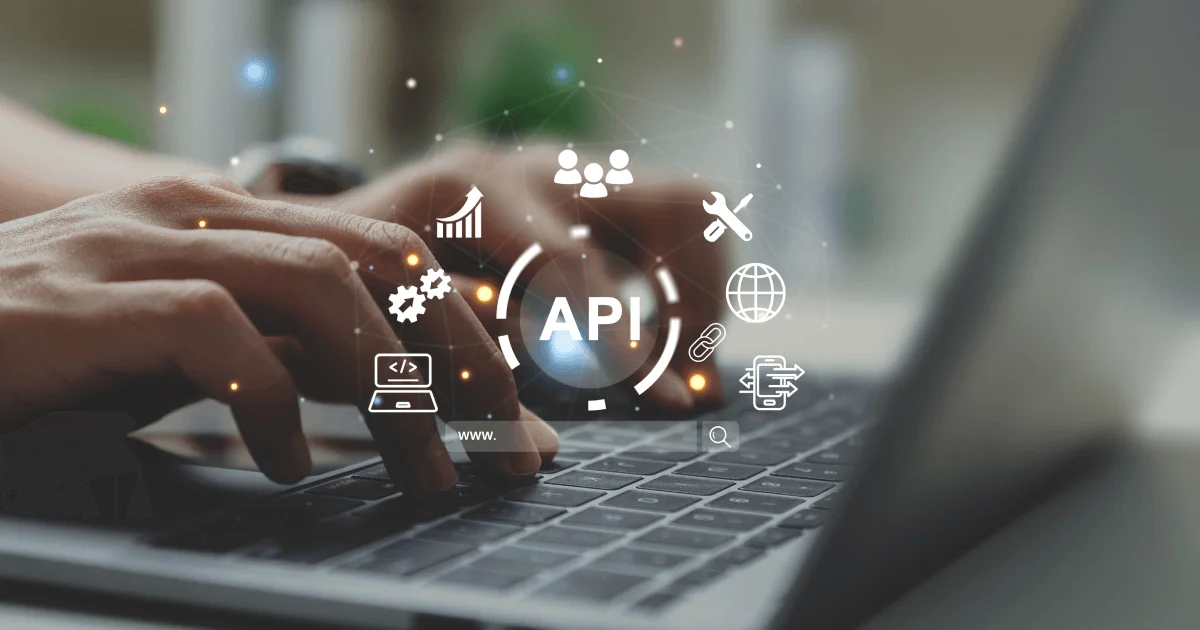
"How can I simplify access to information that already exists within another of my company's applications?"
It's a question that's coming up again and again in the catering industry, both commercial and institutional.
The challenge is to simplify access to information by sharing it automatically, without having to re-enter it.
In the age of data, every company now knows that automating data and data sharing makes it possible to :
That's why it's essential to integrate your organization's various applications.
In the food sector, this need is particularly acute.
The recovery of information crucial to food safety and health standards is essential. This includes, for example, delivery notes, audit results, action plans, data from temperature sensors, product information, as well as certain personal data (first name, surname, etc.) of employees.
At the same time, it is just as important to send certain information to head office, such as traceability data, results of HACCP self-checks, non-compliances detected and any other data from SOP, particularly for integration into Business Intelligence tools.
HACCP applications must offer the flexibility needed to meet these requirements. The use of connectors such as APIs (Application Programming Interfaces) is central to this approach. These APIs can be available as standard, or custom-developed to meet specific needs.
In fact, there are two categories of API in the integration solutions landscape.
On the one hand, there are the "ready-to-use" APIs, which offer standardized functionality, enabling rapid and easy integration between applications. They are generally adapted to generic, well-defined needs, such as connecting to platforms widely used in the industry or executing basic functionality, enabling rapid deployment without complex customization.
On the other hand, some situations call for more customized solutions. For these cases, bespoke APIs are developed, tailored specifically to the unique requirements of one's business, ensuring a precise match with the organization's specific processes and needs.
In short, APIs save considerable time and ensure data reliability by automating and standardizing integration processes between your different applications.
Here are a few concrete examples from the sector to better understand this dynamic.
The aim is to enable complete digitization of delivery notes in conjunction with the CAPM application.
With systems such as Eezytrace, each morning the on-site user receives a detailed overview of the day's deliveries, including the list of items to be received and their respective quantities.
Thanks to this integration on their tablet in their HACCP application, users can not only conduct their quality checks efficiently, but also accurately record quantities received or rejected.
This digitalization facilitates the transmission of information in real time, enabling your supplier invoicing teams to have access to the relevant data even before the delivery driver leaves the site.
This process optimizes not only incoming goods management, but also invoicing.
Keeping track of audits, laboratory analyses and action plans is a real challenge for quality teams and site managers.
The aim is to simplify this process by making all audit and analysis reports, including non-conformities, automatically available in the HACCP software, while enabling effective monitoring of the associated action plans.
Such APIs are now available with modern HACCP solutions such as Eezytrace. These applications are able to connect directly to inspection and analysis organizations via dedicated APIs.
These digital connections facilitate the integration of data and reports in real time, enabling you and your teams to react promptly and knowledgeably to the results of audits and analyses, while ensuring rigorous follow-up of action plans.
The adoption of HACCP software by new users is often accompanied by a desire to retain the automatic temperature sensors already installed in cold rooms or refrigerated display cabinets. The aim is to maintain these existing systems, while centralizing temperature data and corresponding graphics in a unified solution.
By opting for an advanced self-checks digitalization solution, you can not only maintain your current sensor infrastructure, but also benefit from seamless data integration into your HACCP application. Thanks to an "IoT API", temperature data from third-party systems are integrated directly into the application. This enables:
This process is not limited to maintaining an existing sensor system; it also offers the flexibility of choosing a new system if required.
Ultimately, it means significant time savings on a daily basis for on-site users, by simplifying and automating the collection and management of temperature data.
In the foodservice sector, most companies already have dedicated reporting teams, using pre-established Business Intelligence tools (such as Power BI, Tableau...).
Food Quality and Safety management, being crucial pillars of brand image, requires rigorous monitoring and precise steering of operational data from restaurants. The aim is to support best hygiene practices and manage food risk across the entire company.
In this context, modern HACCP applications are invaluable allies. They are equipped with a "Data API" designed to seamlessly transmit all data from self-checks directly to your Data teams.
This integration enables teams to remain autonomous in the management of their operational excellence, by providing them with the means to process and analyze data efficiently, within their existing Business Intelligence environment.
In short, the integration of an advanced HACCP application such as Eezytrace offers a multitude of significant advantages. These platforms feature remarkably flexible APIs, facilitating not only efficient, but also highly adaptive self-checks management. This feature enables seamless integration into your company's pre-existing technological architecture.
As a direct consequence of this seamless integration, companies equipped with the system are seeing a significant strengthening of Food Safety at global level. This benefit is accompanied by enhanced risk control and management, guaranteeing optimum safety and compliance within catering establishments.
To go further in risk management, download our step-by-step guide of 36 pages. (Available in English soon)