TotalEnergies chooses Eezytrace to ensure Food Safety in its stations around the world
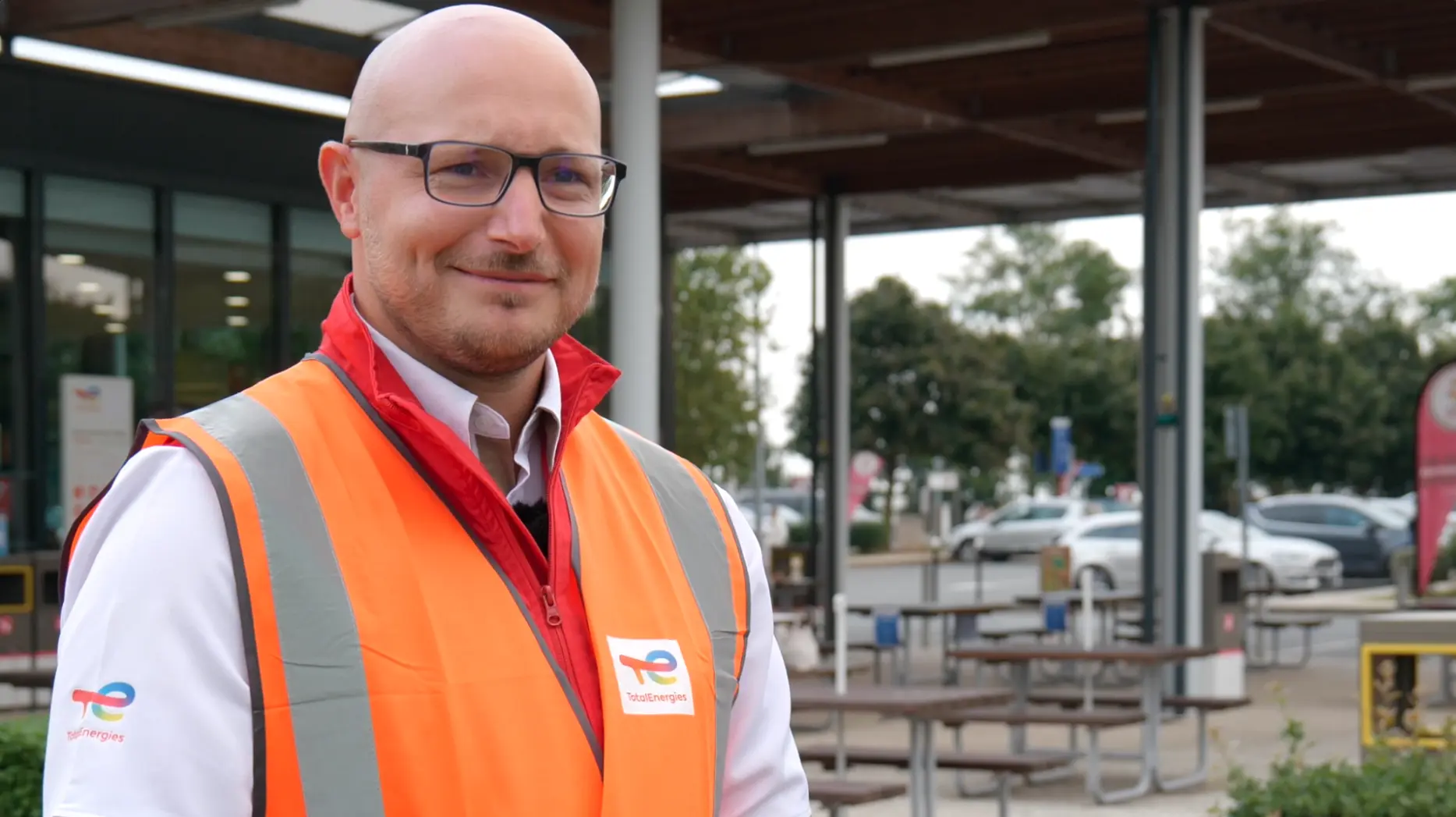
Rémy Gibeaux:In our stations, food safety shows up through numerous checks, such as the condition of incoming goods, temperature monitoring in refrigerated storage rooms several times a day, as well as daily, weekly and monthly cleaning schedules, daily inventory of expired products, and daily recordings to trace ingredients used in catering.
All these checks were previously carried out manually, with a notebook and a pen! We definitely needed an innovative solution to ease task management and secure storage, which is a critical point: these data may be requested by the authorities in the event of an inspection, or even a health crisis.
By the end of 2019, we launched the Dig'EAT project with a panel of 12 suppliers. After a testing phase with 3 of them in 3 different countries, and listening to user satisfaction, we opted for the Eezytrace solution, which is developed by Eeworx and deployed in partnership with SGS, World Leader in inspection, control, analysis and certification. The application is available on Android tablets with a photo function, and paired with a printer and temperature sensors. The solution allows easy self-checks and real-time management thanks to a simple and intuitive graphic interface, with a back office available 24/7 for managers and local advisors.
RG: There are many. Automatic configurations in every check facilitate task management on a daily basis. Records are secured throughout the food chain. In each station, the staff save precious time - around 2 hours a day - and we notice a reduction in losses thanks to automatic alerts regarding temperature deviations and expiring products.
Once the stations go digital, they would not go back to paper! The solution improves SOPs and Non Compliance Monitoring, and provides assistance with daily tasks and management. As far as Support and Management teams are concerned, Eezytrace allows easy activity management and problem identification, while improving history access, reporting, and standard and instruction updates.
To go further in risk management, download our step-by-step guide of 36 pages. (Available in English soon)